Mark Bury & Carlito Cascone
Master Builders Solutions US & Canada
Introduction
Concrete, once mixed, starts a rapid process of hydration, where water reacts with cement to make it set and harden. This transformation, while critical, creates a limited window of time to transport, place, and finish the concrete. Extending this window can help overcome challenges related to long-haul transportation, project delays, and other logistical issues.
Hydration-control admixtures, used at low doses, can temporarily pause the hydration process, keeping concrete in a plastic state for extended periods. Higher doses allow unused concrete to remain fluid long enough to be recycled into new batches. This blog explores the science and sustainability advantages of hydration-control admixtures (HCAs) in concrete, culminating in a groundbreaking experiment in which stabilized concrete traveled coast to coast across the U.S., staying fluid and ready to use.
Coast-to-Coast Experiment: Testing the Limits of Hydration Control
To evaluate hydration control’s true potential, an ambitious experiment aimed to keep concrete fluid for seven days while transporting it from Eastport, Maine, to San Francisco, California. This journey required lab tests to ensure that the concrete, dosed with an HCA, could stay workable for extended periods.
Laboratory Feasibility Study Three mixtures were tested to determine the best proportions for the trip, with a mix ratio of 25% stabilized recycled concrete and 75% fresh concrete producing optimal results. The mix details are shown below: The following results came from the study of the fresh concrete after the cross-country trip.
Concrete Mixture Composition | Reference mixture | 1-week hydration-controlled mixture | 75% fresh concrete + 25% returned concrete mixture |
---|---|---|---|
Type IL portland cement, lb/yd³ (kg/m³) | 705 (418) | 705 (418) | 529 (314) |
Coarse aggregate, lb/yd³ (kg/m³) | 1,584 (940) | 1,583 (939) | 1,188 (705) |
Fine aggregate, lb/yd³ (kg/m³) | 1,296 (769) | 1,295 (768) | 972(577) |
Returned concrete, lb/yd³ (kg/m³) | - | - | 984 (584) |
Water, lb/yd³ (kg/m³) | 353 (209) | 353 (209) | 264 (157) |
Water-reducing admixture, fl oz/cwt (mL/100kg) cement | 1 (0.65) | 1 (0.65) | - |
Hydration-controlling admixture, fl oz/cwt (mL/100kg) cement | - | 90 (58.5) | - |
High-range water-reducing admixture, fl oz/cwt (mL/100kg) cement | - | - | 3 (1.95) |
Set accelerating admixture, fl oz/cwt (mL/100kg) cement | - | - | 60 (39) |
Strength enhancing admixture, fl oz/cwt (mL/100kg) cement | - | - | 40 (26) |
Synthetic Fiber, lb/yd³ (kg/m³) | - | - | 1.5 (0.9) |
Plastic and Hardened Concrete Properties | |||
---|---|---|---|
Slump, in. (mm) | 8.75 (222) | 9.5 (241) | 9.5 (241) |
Air content, % | 1.6 | 2.1 | 1.1 |
28-day compressive strength, psi (MPa) | 6,580 (45) | - | 7,910 (55) |
28-day flexural strength, psi (MPa) | 530 (4) | - | 660 (5) |
Initial setting time, hours | 3.5 | - | 7.8 |
Final setting time, hours | 5 | - | 11.4 |
Lab results highlighted several key findings:
High workability was maintained across all mixtures.
A dosage of 90 fl oz of HCA per 100 kg of cement was effective for one-week fluidity.
Composite concrete mixtures showed higher strength and extended setting time.
These promising lab results paved the way for the cross-country experiment.
Understanding Hydration-Controlling Admixtures
The journey to develop reliable hydration-controlling admixtures began in the 20th century. Early admixtures aimed to delay setting time but often had unpredictable results. The next generation of HCAs brought consistency to this approach, allowing for precise control over the hydration process. A modern HCA allows contractors to schedule with accuracy, improving overall project efficiency. These admixtures meet the ASTM C494/C494M, Type B and Type D standards, providing a predictable delay in setting time without affecting ultimate concrete strength.
Reusing Returned Plastic Concrete
Returned concrete poses a disposal challenge for most construction projects. While some options for reuse exist, such as creating concrete blocks or fill material, they are not always viable. A more sustainable approach is to dose returned concrete with a hydration-controlling admixture, preserving its fluidity and allowing it to be combined with new concrete, as shown in Figure 1.
Figure 1
Durability studies, like that by Senbetta and Bury, have found that using stabilized, returned concrete mixed with fresh concrete does not compromise performance. In fact, several properties, including compressive strength and cracking resistance, are improved. The durability outcomes from a comparative study are summarized below:
Table 2
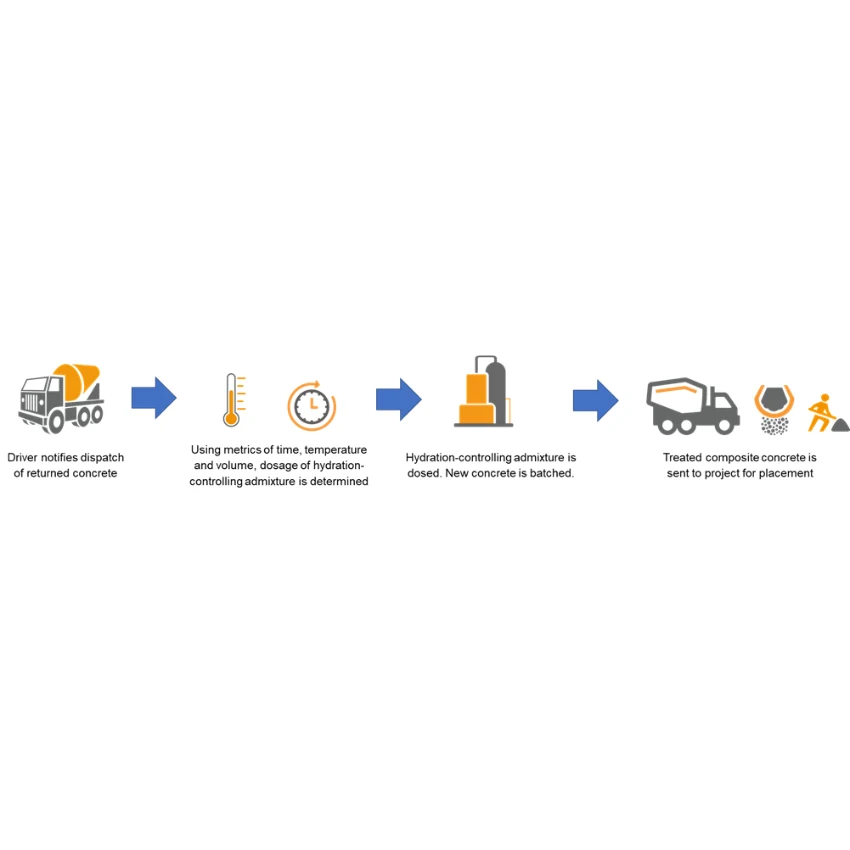
Performance Attribute | Concrete Result Relative to the Reference Concrete | Treated Concrete Comparison |
---|---|---|
Compressive Strength | ||
- 3-Days | +21% | Better |
- 7-Days | +7% | Better |
- 28-Days | +6% | Better |
Freezing and Thawing | 101% of Reference | Similar |
Hardened Air Void Analysis | Good Spacing Factors and Specific Surface | Similar |
Long-Term Corrosion Test | Lower Corrosion Current | Better |
Short-Term Corrosion Test | Stable Passivation Layer | Similar |
Abrasion | +5% | Similar |
Absorption | -5% | Similar |
Permeable Void Volume | -5% | Similar |
Susceptibility to Cracking | 75% Less Potential | Better |
Leveraging Digital Tools for Efficiency
Hydration control for returned concrete has been made more manageable with recent advances in digital tools, including sensors, AI, and real-time data analysis. For example, the MasterAtlas™ platform enables automated monitoring of concrete properties, admixture dosing recommendations, and reporting capabilities for project audits. This digitalization makes tracking and managing returned concrete easier and enhances sustainability efforts by minimizing concrete waste.
Figure 3
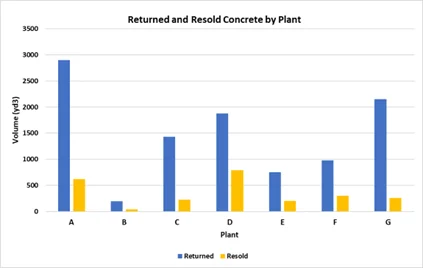
Lab results highlighted several key findings:
High workability was maintained across all mixtures.
A dosage of 90 fl oz of HCA per 100 kg of cement was effective for one-week fluidity.
Composite concrete mixtures showed higher strength and extended setting time.
These promising lab results paved the way for the cross-country experiment.
Day-by-Day Journey Across the U.S.
The stabilized concrete began its journey on the East Coast, and daily measurements of slump and temperature confirmed it remained plastic throughout the trip. Key highlights include:
Day 1-2: Starting in Maine, the concrete was mixed and transported to Seneca Falls, NY. Measurements confirmed it remained fluid.
Day 3-5: Passing through Chicago and Mount Rushmore, minor stiffness was observed due to settling but was easily remedied by stirring.
Day 6-7: The concrete arrived in San Francisco after traveling over 4,000 miles, remaining in a plastic state ready for testing.
Figure 4
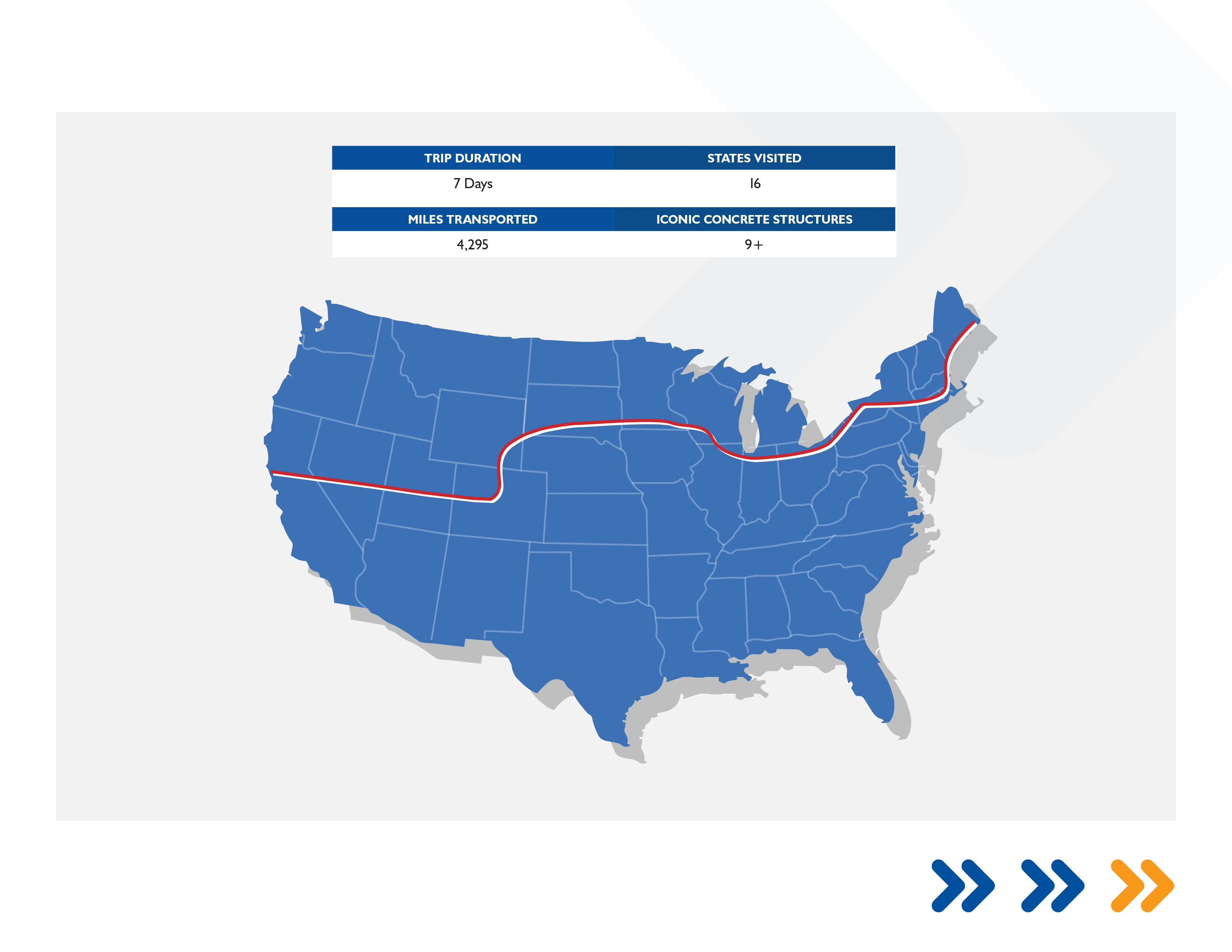
At the end of the journey, the concrete was tested for recyclability by mixing it with fresh concrete. The resulting composite showed strong performance in compressive tests, proving that concrete could be preserved for long hauls without loss of quality.
Figure 5
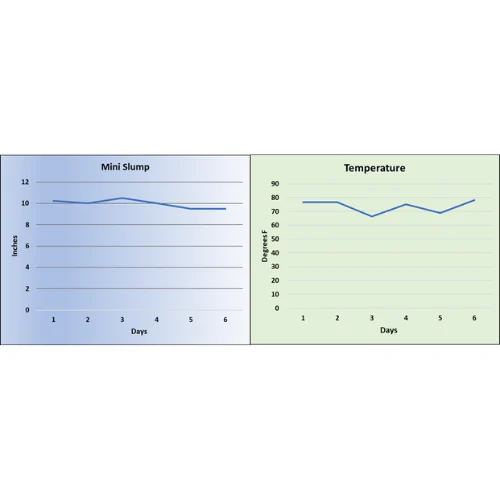
Sustainable Impact of Hydration Control
The successful reuse of stabilized concrete contributes significantly to sustainability by reducing landfill waste and CO₂ emissions. Tables 4 and 5 below illustrate the potential emissions savings and landfill diversion achievable by recycling returned concrete at different production levels.
Table 4
Annual Production (yd³) | Returned Concrete (yd³) | Annual CO₂ Emissions Savings (lb) |
---|---|---|
60,000 | 2,4000 | 1,619,352 |
50,000 | 2,000 | 1,349,460 |
40,000 | 1,600 | 1,079,568 |
30,000 | 1,200 | 809,676 |
20,000 | 800 | 539,784 |
10,000 | 400 | 269,892 |
Table 5
Fresh to Recycled Concrete Ratio | CO₂ Emissions Savings (lb/10 yd³) | CO₂ Emissions Savings (kg/7.65 m³) |
---|---|---|
90:10 | 675 | 306 |
80:20 | 1,349 | 612 |
70:30 | 2,024 | 918 |
60:40 | 2,699 | 1,224 |
50:50 | 3,374 | 1,530 |
Conclusion
The coast-to-coast experiment demonstrates the power of hydration control to extend the plastic state of concrete. This technology has far-reaching implications for the construction industry:
Extended Transport and Flexible Placement: Construction teams can now transport concrete over long distances without compromising usability.
Waste Reduction: Hydration control allows for effective reuse of returned concrete, minimizing waste and reducing landfill use.
Sustainable Construction Practices: Recycling concrete in a new batch reduces CO₂ emissions and maximizes resource efficiency.
This experiment underscores how hydration control, set-control, strength-enhancing, and concrete-conditioning admixtures are paving the way for more sustainable, resilient construction practices.
For more information contact: mark.bury@masterbuilders.com